The Problem
Frequent machinery breakdowns due to a lack of structured maintenance and manual tracking have resulted in significant production losses for the manufacturing company. This indicates a reactive approach to maintenance, which is inefficient and costly.
Solution: Preventive Maintenance Program (PMP) and Predictive Maintenance Tools (PMT) or Computerized Maintenance Management System (CMMST)
A well-structured Preventive Maintenance Program (PMP) combined with the capabilities of Predictive Maintenance Tools (PMT) or a Computerized Maintenance Management System (CMMST) can effectively address these issues.
Preventive Maintenance Program (PMP)
A PMP involves scheduled inspections, repairs, and replacements of equipment to prevent failures. It focuses on preventing breakdowns rather than reacting to them.
Benefits of PMP:
Increased equipment lifespan: Regular maintenance extends the life of machinery.
Reduced unplanned downtime: By addressing potential issues proactively, production disruptions are minimized.
Lower repair costs: Early detection of problems leads to less expensive repairs.
Improved safety: Regular inspections identify potential safety hazards.
Optimized production: Consistent equipment performance contributes to higher output.
Predictive Maintenance Tools (PMT) or Computerized Maintenance Management System (CMMST)
These tools provide data-driven insights into equipment health and help optimize maintenance activities.
Benefits of PMT/CMMST:
Real-time monitoring: Sensors collect data on equipment performance, allowing for early detection of anomalies.
Predictive analytics: By analyzing data, potential failures can be predicted before they occur.
Optimized maintenance scheduling: Maintenance tasks can be prioritized based on equipment condition.
Improved resource allocation: Maintenance resources can be allocated efficiently.
Data-driven decision making: Insights from data help in making informed maintenance decisions.
How PMP and PMT/CMMST Work Together
A PMP provides a framework for routine maintenance, while PMT/CMMST adds intelligence to the process.
Equipment data collection: Sensors collect data on equipment performance, such as vibration, temperature, and pressure.
Data analysis: PMT/CMMST analyzes the data to identify patterns and predict potential failures.
Maintenance scheduling: Based on the analysis, maintenance tasks are scheduled proactively.
Work order generation: The system generates work orders for maintenance technicians.
Inventory management: Required spare parts are automatically ordered.
Performance monitoring: The system tracks equipment performance and maintenance history.
Overall Impact
By implementing a PMP and leveraging PMT/CMMST, the manufacturing company can:
Significantly reduce unplanned downtime and production losses.
Improve equipment reliability and lifespan.
Optimize maintenance costs and resource allocation.
Enhance safety by identifying potential hazards early.
Make data-driven decisions to improve overall operational efficiency.
By shifting from a reactive to a proactive maintenance approach, the company can achieve substantial improvements in productivity and profitability.
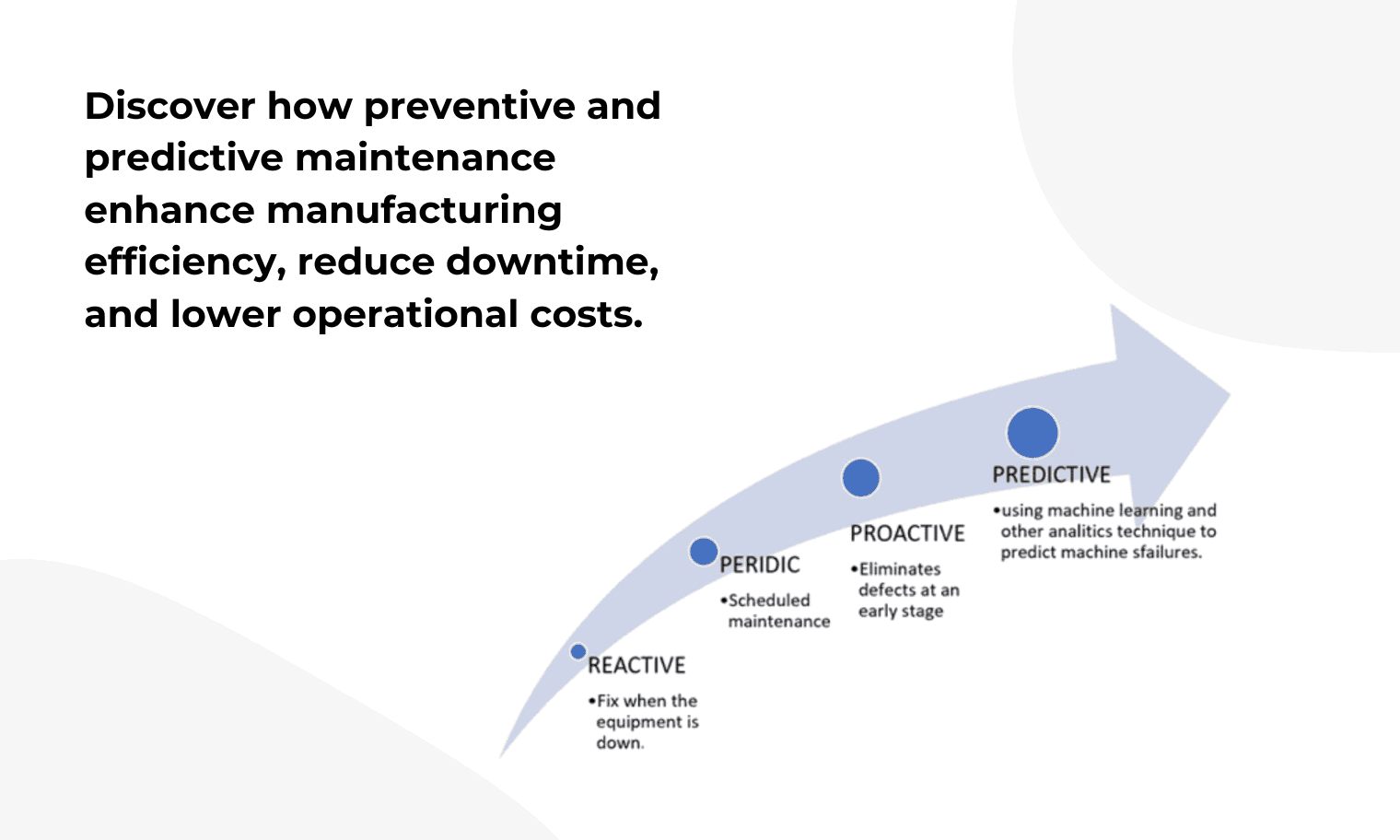
Implementing a Preventive Maintenance Program (PMP)
Implementing a PMP can be a complex process, but with careful planning and execution, it can yield significant benefits. Let's break down the key steps involved:
1. Conduct a Comprehensive Equipment Assessment
Identify critical equipment: Determine which machinery is essential for production.
Gather equipment data: Collect information on equipment age, operating hours, maintenance history, and failure rates.
Perform failure mode and effects analysis (FMEA): Identify potential failure points and their consequences.
2. Develop a Maintenance Schedule
Determine maintenance intervals: Based on equipment data and manufacturer recommendations, set up a maintenance schedule.
Prioritize tasks: Identify critical tasks that must be performed regularly and less critical ones.
Allocate resources: Assign personnel and equipment to carry out maintenance activities.
3. Create Detailed Maintenance Procedures
Develop step-by-step instructions: Clearly outline procedures for each maintenance task.
Include safety guidelines: Ensure personnel safety during maintenance activities.
Standardize procedures: Create consistent processes across the organization.
4. Assemble a Skilled Maintenance Team
Identify required skills: Determine the necessary expertise for the maintenance team.
Provide training: Offer training on equipment operation, maintenance procedures, and safety.
Encourage continuous learning: Foster a culture of ongoing skill development.
5. Implement a Spare Parts Management System
Identify critical spare parts: Determine which parts are essential for equipment operation.
Establish inventory levels: Maintain adequate stock of spare parts to minimize downtime.
Implement a tracking system: Monitor spare part usage and replenish inventory as needed.
6. Implement a CMMS or Maintenance Software
Select appropriate software: Choose a system that aligns with your organization's needs.
Data entry: Input equipment information, maintenance schedules, and spare parts data.
Work order management: Create and manage work orders efficiently.
Performance tracking: Monitor maintenance KPIs and generate reports.
7. Gain Buy-in from All Stakeholders
Communicate the benefits: Explain how PMP will improve productivity and reduce costs.
Involve employees: Seek input from operators and maintenance personnel.
Provide training: Educate employees about the PMP and their role in its success.
8. Monitor and Evaluate Performance
Track key performance indicators: Measure equipment uptime, maintenance costs, and repair frequency.
Analyze data: Identify trends and areas for improvement.
Make adjustments: Modify the PMP as needed to optimize performance.
Overcoming Challenges
Resistance to change: Address concerns and communicate the benefits of PMP.
Budget constraints: Prioritize maintenance activities and allocate resources effectively.
Lack of skilled personnel: Provide training and consider outsourcing certain tasks.
Data management: Implement a robust CMMS to streamline data collection and analysis.
By following these steps and addressing potential challenges, you can successfully implement a PMP that enhances equipment reliability, reduces downtime, and improves overall operational efficiency.

Key Components of a Preventive Maintenance Program (PMP)
A robust PMP is essential for maximizing equipment uptime and minimizing unexpected breakdowns. The core components include:
1. Equipment Inventory and Assessment
Comprehensive equipment list: Detailed inventory of all machinery and assets.
Criticality assessment: Identifying equipment based on importance to production.
Failure history analysis: Reviewing past breakdowns to identify patterns and trends.
2. Maintenance Task Development
Task identification: Determining necessary maintenance activities for each equipment.
Task scheduling: Establishing frequencies for inspections, replacements, and overhauls.
Standard operating procedures (SOPs): Creating detailed guidelines for maintenance tasks.
3. Spare Parts Management
Critical spare parts identification: Determining essential components to keep in stock.
Inventory levels: Maintaining optimal spare parts inventory to avoid shortages.
Supplier management: Establishing reliable relationships with suppliers.
4. Maintenance Workforce
Skill assessment: Evaluating the skills and knowledge of maintenance personnel.
Training and development: Providing necessary training to enhance capabilities.
Workload management: Balancing workload to prevent burnout and errors.
5. Performance Monitoring and Improvement
Key performance indicators (KPIs): Defining metrics to measure PMP effectiveness.
Data collection: Gathering data on maintenance activities, equipment performance, and costs.
Continuous improvement: Analyzing data to identify areas for improvement and implementing changes.
6. Documentation
Maintenance history: Maintaining detailed records of all maintenance activities.
Equipment manuals: Storing technical documentation for reference.
PM schedules: Documenting planned maintenance tasks and their frequencies.
By carefully considering these components and implementing them effectively, organizations can establish a solid foundation for their preventive maintenance program, leading to improved equipment reliability and overall operational efficiency.
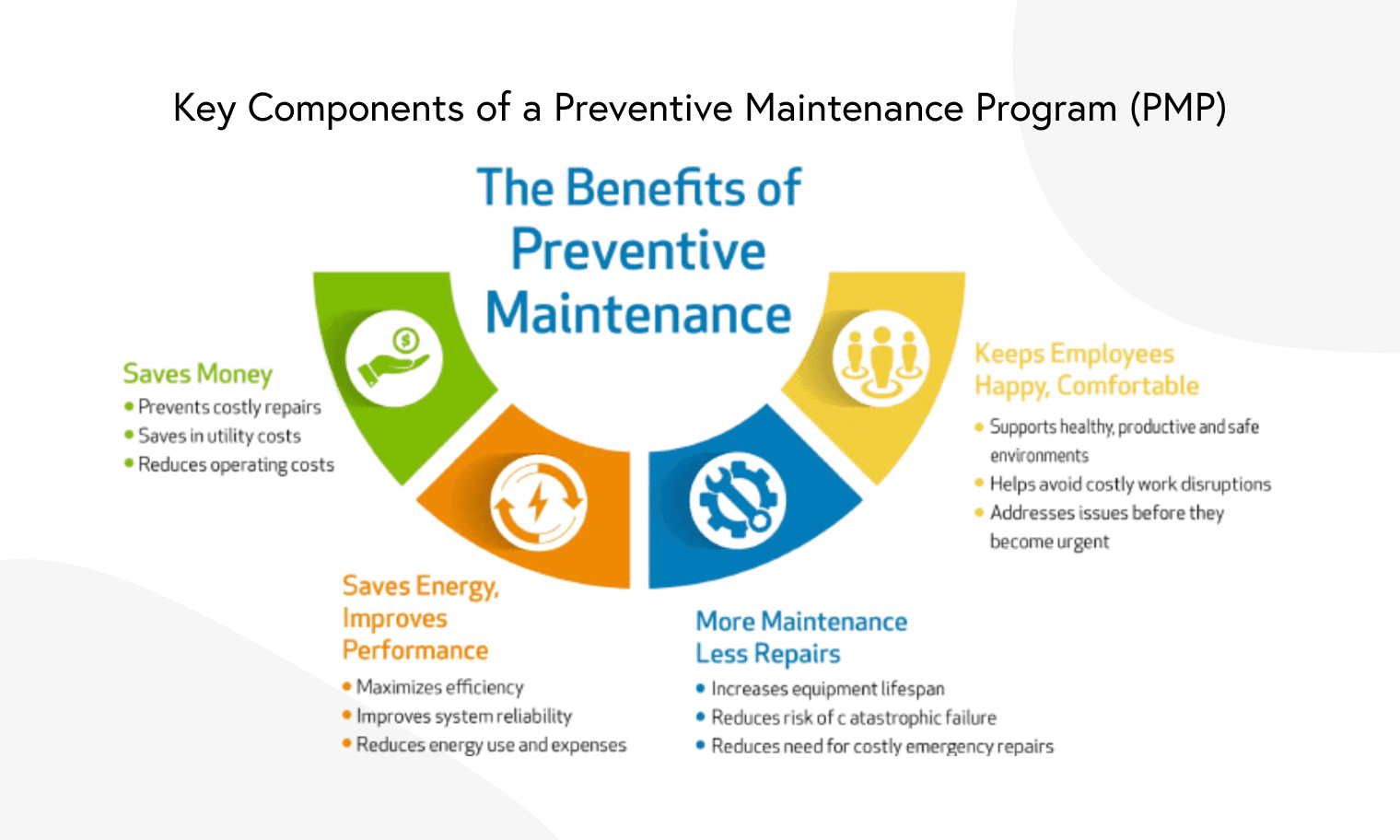
Integrating Preventive Maintenance (PM) and Predictive Maintenance (PdM)
Combining Preventive Maintenance (PM) and Predictive Maintenance (PdM) creates a powerful synergy that optimizes equipment reliability and reduces maintenance costs.
Understanding the Synergy
PM establishes a baseline: Regular inspections and maintenance tasks provide a foundation for equipment health.
PdM refines the baseline: By analyzing real-time data, PdM identifies anomalies and predicts potential failures, optimizing PM intervals.
Optimized resource allocation: PdM helps prioritize maintenance tasks, ensuring resources are focused on equipment with the highest risk of failure.
Enhanced decision making: Combining historical PM data with predictive insights improves maintenance strategies.
Key Integration Strategies
Data-driven PM adjustments: Use PdM data to modify PM schedules and tasks based on equipment condition.
Condition-based monitoring integration: Incorporate PdM sensors into PM routines for early detection of issues.
Risk-based maintenance: Prioritize PM tasks based on PdM-identified risk levels.
Real-time alerts: Trigger PM interventions based on PdM-generated alerts.
Shared data platform: Ensure seamless data exchange between PM and PdM systems.
Benefits of Integration
Increased equipment uptime: By addressing issues before they become critical, unplanned downtime is reduced.
Optimized maintenance costs: Avoid unnecessary PM tasks while preventing costly breakdowns.
Improved resource utilization: Efficient allocation of maintenance personnel and spare parts.
Enhanced asset lifecycle management: Prolonged equipment life through proactive maintenance.
Data-driven continuous improvement: Refine maintenance strategies based on performance metrics.
Example:
Imagine a manufacturing plant with a fleet of industrial robots. A PM schedule might dictate regular lubrication every 1000 hours. However, PdM analysis reveals that vibration sensors indicate a specific robot's lubrication is deteriorating faster than expected. By integrating PM and PdM, maintenance can be scheduled earlier for that robot, preventing potential breakdowns and extending its lifespan.
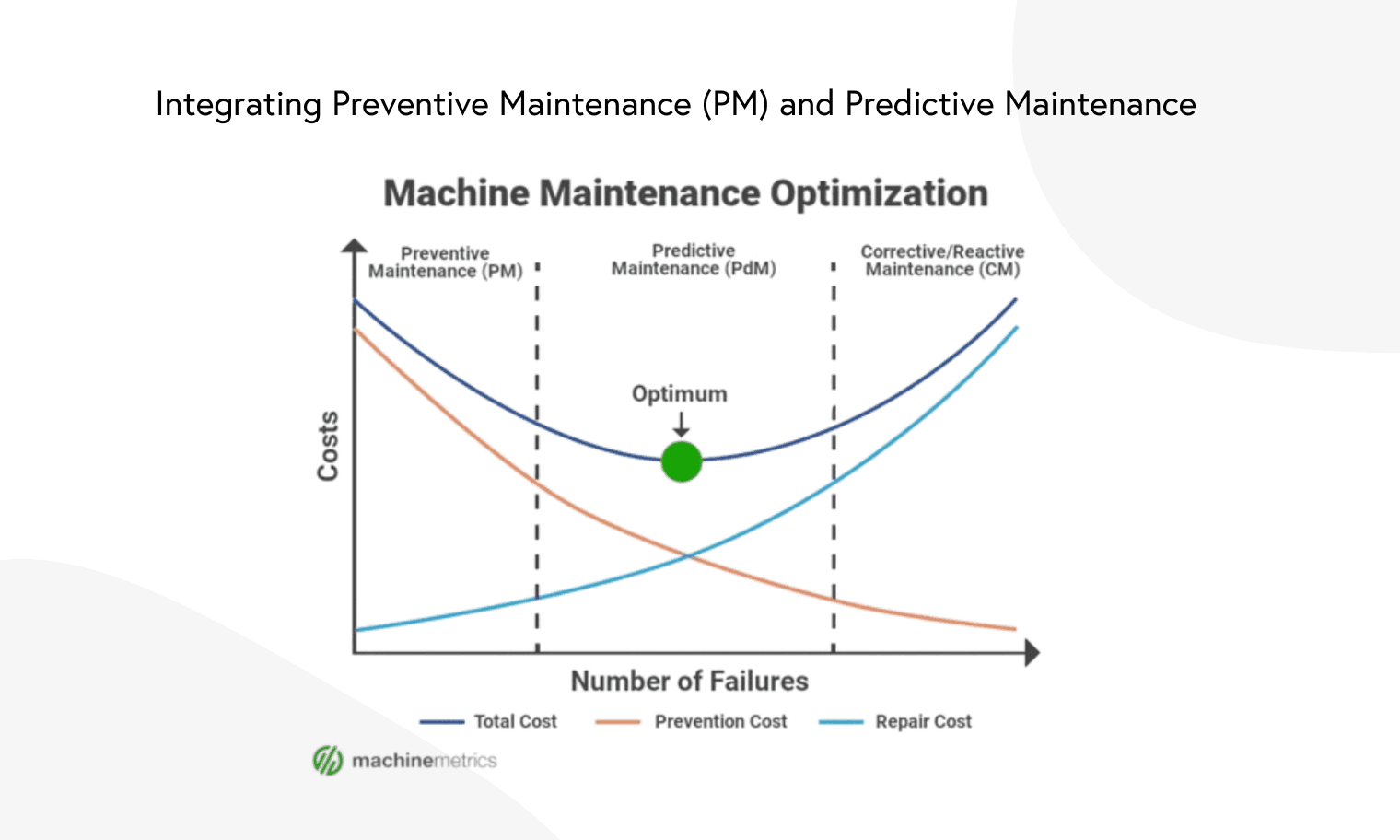